Commercial building demolition is more than just tearing down structures; it’s about doing so safely, efficiently, and in compliance with all relevant regulations. Its scale is often much higher than that of a residential demo job and can be intense to manage once the job has been green-lit. Whether the project is driven by structural instability, renovation plans, or the need to repurpose space, a successful demolition requires careful planning and execution.
Whether dealing with office buildings, retail spaces, warehouses, or hotels, the following considerations and implementations we’ll touch on in this blog will ensure that any commercial demolition process is carried out responsibly and effectively from the start.
6 Types of Commercial Building Demolition
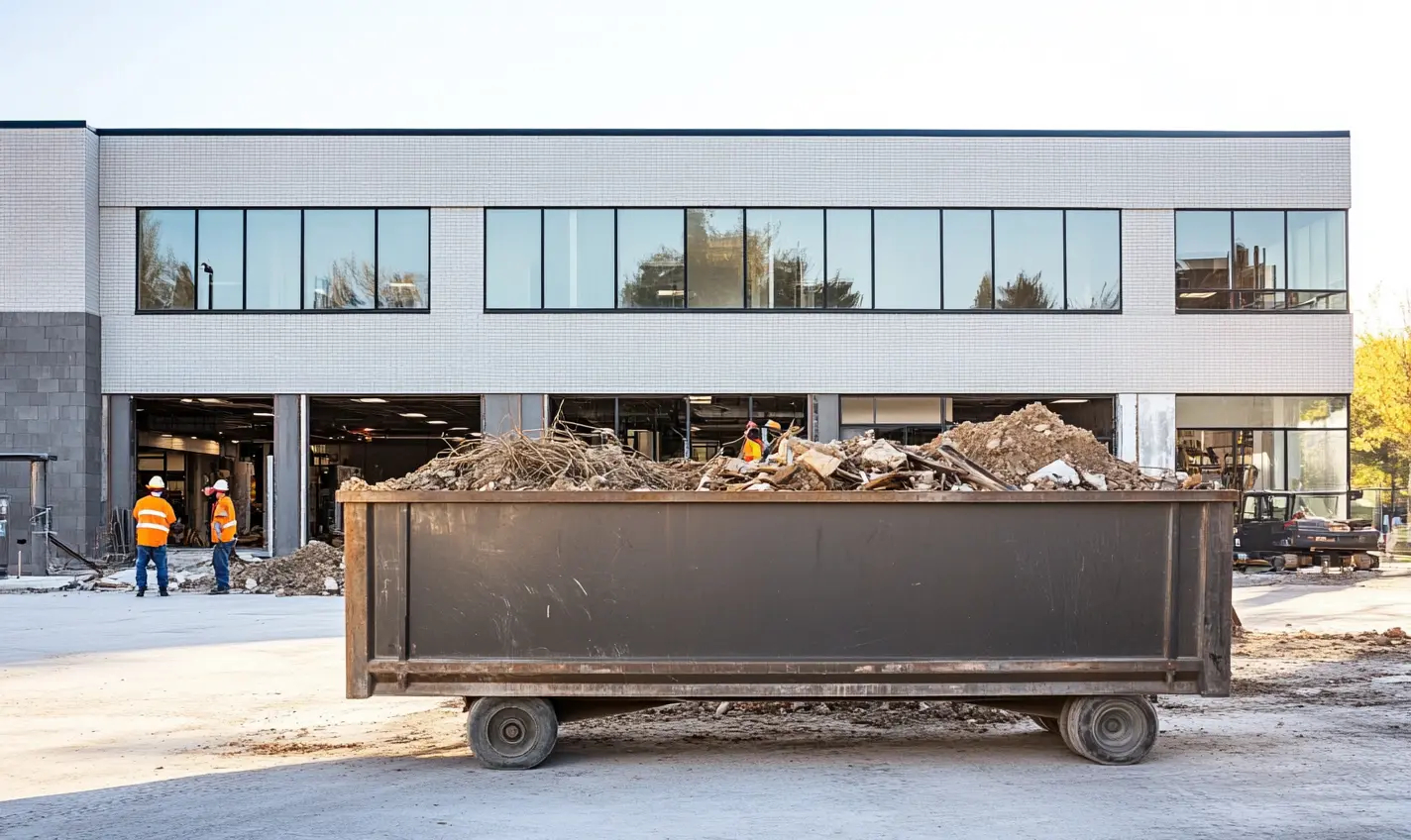
The method of demolition chosen for a project depends on several factors, including the building’s size, location, and the desired outcome. Demolition can range from all sizes for commercial jobs depending on what the client wants, therefore it’s important to be familiar with the definitions of what will be taking place and make sure the focus of the project is clear between the client and the crew hired:
- Mechanical Demolition: The most common method of demo, mechanical demolition involves the use of heavy machinery like excavators, bulldozers, and wrecking balls to systematically dismantle the structure. This is a full scale demo and reserved for large scale projects that go beyond remodeling.
- Selective Demolition: For projects where specific parts of the building need to be preserved or recycled, selective demolition is ideal. This approach minimizes disruption and allows for the careful removal of materials.
- Deconstruction: A more labor-intensive method, deconstruction involves the manual disassembly of a building to maximize material recovery and recycling. This technique aligns well with sustainability goals and can be cost-effective in the long run.
- Interior Demolition: Often used in renovations, interior demolition focuses on gutting the inside of a building while preserving the external structure. It’s a precise method that allows for significant changes to a building’s layout without altering its overall form.
- Implosion Demolition: This technique involves strategically placed charges to collapse a building inward. It’s a dramatic method typically reserved for large, complex structures, especially in urban settings where space is limited.
- Crane and Ball Demolition: Although less common today, this method involves a wrecking ball attached to a crane to bring down large structures quickly. It’s effective for broad-scale destruction but requires careful planning to avoid collateral damage.
Factors Influencing Commercial Demolition Costs & What to Budget For
Several factors influence the cost of commercial building demolition, and understanding these can help in accurate budgeting and planning:
- Building Size and Complexity: Larger and more complex buildings require additional resources, time, and specialized equipment, which can drive up costs. Complex structures may also require more detailed planning and safety measures.
- Hiring Solid Labor: Skilled labor and equipment operators are vital to executing the demolition safely and efficiently. This shouldn’t be overlooked when looking to get a job done within the expected time, cleanly, and without accidents that can lead to losing money.
- Location: Urban areas often present higher costs due to stricter regulations, limited access, and the need to minimize disruption to surrounding properties. Remote locations might incur additional transportation costs for equipment and materials.
- Materials Used: Buildings constructed with hazardous materials, such as asbestos or lead, require specialized handling and disposal procedures. These materials not only increase costs but also necessitate compliance with stringent safety regulations.
- Disposal Fees: The cost of disposing of waste materials varies depending on the type and volume of debris. Recycling fees, landfill charges, and transportation costs all contribute to the overall expense.
- Permits and Regulations: Navigating the complex web of local, state, and federal regulations can add to the cost. Obtaining permits, conducting necessary inspections, and ensuring compliance with environmental and safety standards are essential but can be costly and time-consuming.
- Safety Measures: Implementing extensive safety protocols and providing protective equipment for workers are necessary expenses to ensure the safety and compliance of the demolition project. Investing in personal protective equipment (PPE), including masks, gloves, protective goggles, safety helmets, and appropriate work clothing is a must, not only for the well being of your employees, but for passing regular safety checks from supervisors.
- Additional Services: Certain projects may require specialized services such as asbestos removal, site grading, or utility disconnections. These services are essential for a safe and compliant demolition process.
- Contingency Fees: The one nobody wants to think about budgeting for. Unforeseen complications can arise during demolition, so it’s wise before bidding a job to analyze potential risks and determine if you can allocate a portion of the budget for unexpected expenses and possible errors.
Step-by-Step Demolition Procedures
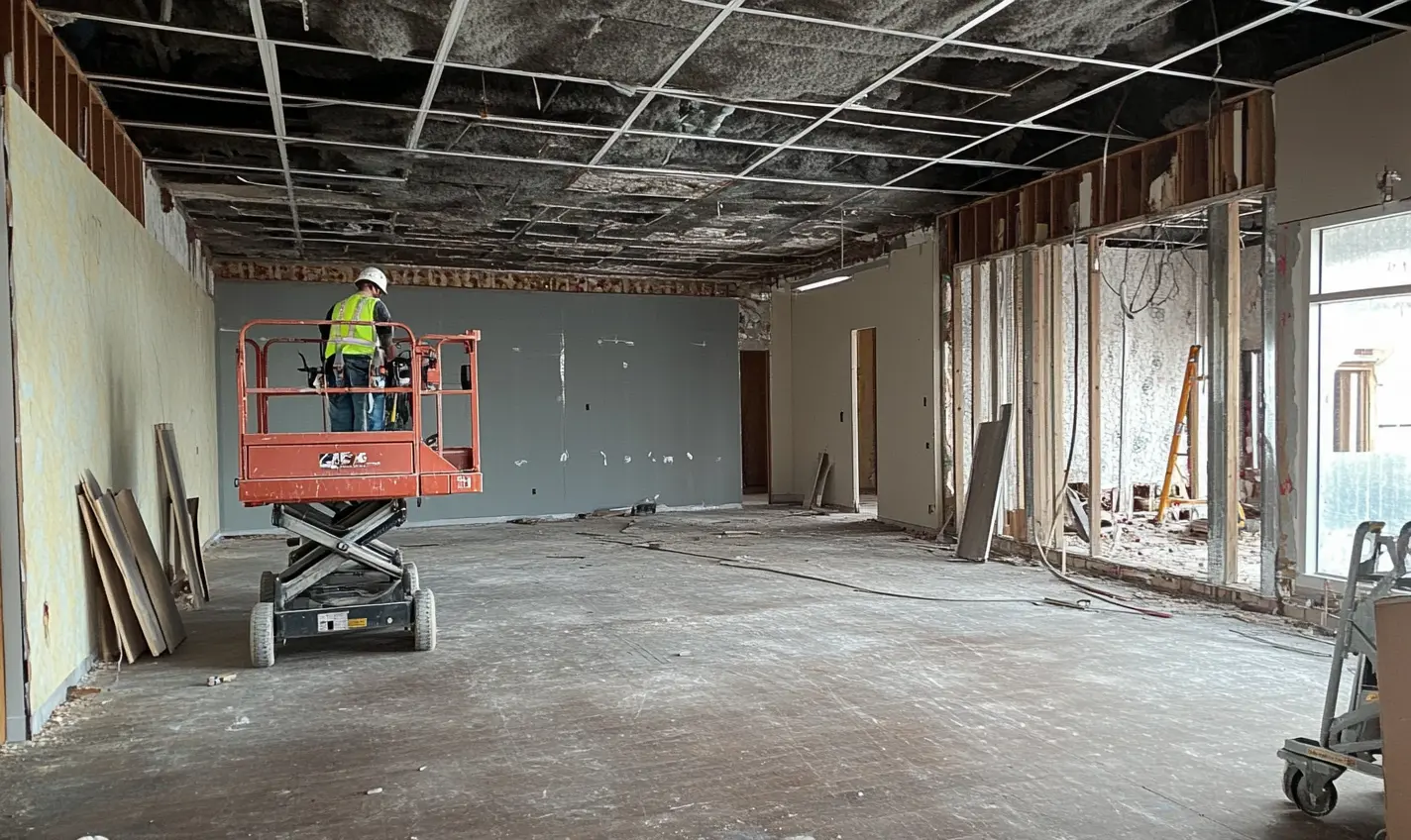
A successful demolition project follows a well-structured process:
- Site Inspection and Planning: The first step is a thorough inspection of the site, identifying potential hazards and structural challenges. This stage also involves developing a comprehensive demolition plan that outlines the procedures, safety measures, and resource allocation.
- Asbestos and Hazardous Material Removal: If hazardous materials such as asbestos are present, they must be safely removed in accordance with regulations. This step is crucial for protecting workers and preventing environmental contamination.
- Shutoff Utilities: Before demolition begins, all utilities—such as electricity, gas, and water—must be disconnected safely. Coordinating with utility providers ensures that there are no risks of leaks or electrical hazards during the demolition process.
- Structural Demolition: The core of the project involves systematically dismantling the building, starting with non-load-bearing elements and progressing to the main structure. Do not get too greedy with what you choose to budget for and what not - The use of appropriate machinery and techniques ensures the demolition is carried out efficiently and safely.
- Debris Removal and Site Cleanup: Once the building is demolished, debris removal and site cleanup are essential. Materials are sorted for recycling or proper disposal, and the site is prepared for its next phase, whether that’s new construction or another purpose.
Following these steps ensures that the demolition is completed safely, on time, and within budget.
Conclusion and Key Takeaways
Commercial building demolition is a complex process that requires a blend of careful planning, execution, and strict adherence to regulations. From choosing the appropriate demolition method to managing costs and ensuring safety, each aspect of the project plays a crucial role in its overall success.
Key takeaways include the importance of selecting the right demolition method, understanding the factors that influence costs, and following a detailed, step-by-step process to ensure a smooth project. Regulatory compliance and safety considerations are also essential, protecting both workers and the environment.
For professional demolition services in and around Bend, OR, or Atlanta, GA, Swift Demo is here to help. Contact us at 541-306-3360 or email us at hello@swift-demo.com for expert assistance with your demolition projects. We guarantee thorough preparation, accurate estimates, safe execution and a DUST-FREE final sweep for every job.
Related Blogs
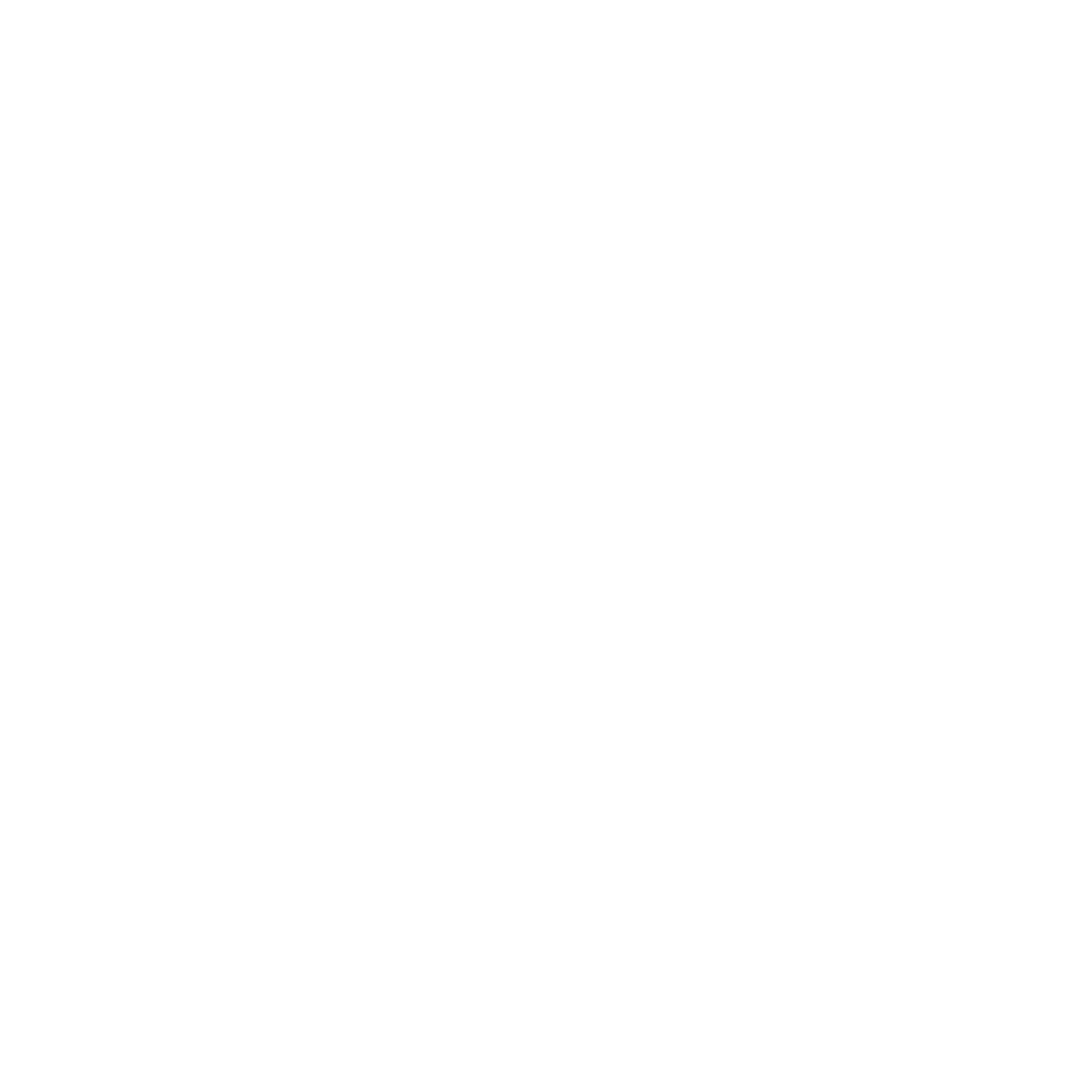